Alümina seramikler, metallere kıyasla 3-10 kat daha uzun aşınma ömrü sunarak zorlu endüstriyel uygulamalarda arızaları ve duruş sürelerini önemli ölçüde azaltır. Üstün dayanıklılıkları, bakım sıklığını ve toplam sahip olma maliyetini (TCO) doğrudan azaltır.
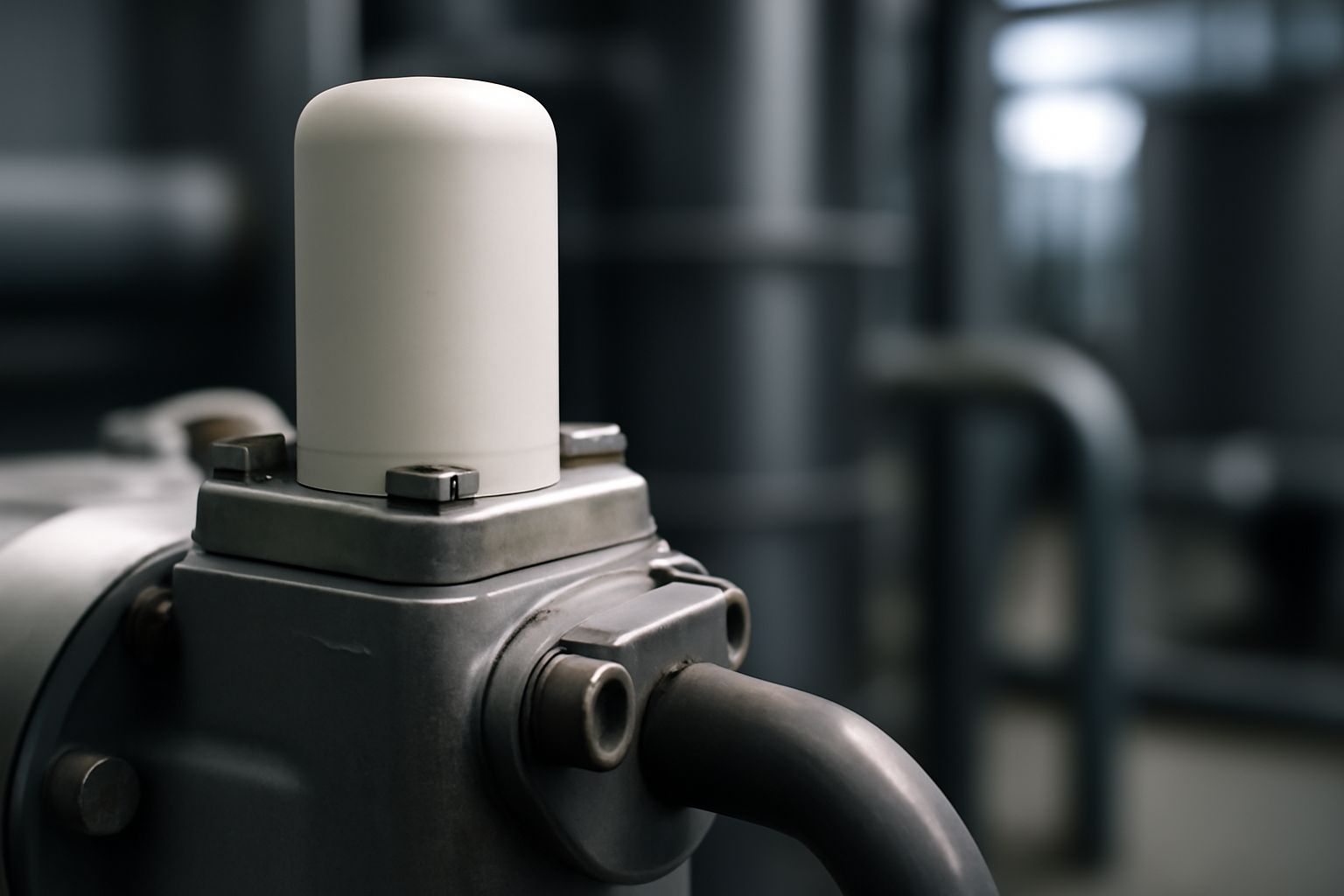
Kritik Ortamlarda Alümina Parçalar Neden Metallerden Daha Üstündür?
Zorlu endüstriyel ortamlarda, alüminyum oksit seramik, olağanüstü sertliği, yüksek saflığı ve aşınma ve korozyona karşı direnci sayesinde metal alaşımlarından daha iyi performans gösterir. Paslanmaz çelik veya sertleştirilmiş alaşımlarla karşılaştırıldığında, **alümina seramik** parçalar Aşındırıcı, yüksek sıcaklıklı veya aşındırıcı işlemlerde binlerce döngüden sonra boyutsal kararlılığı korur. Bu güçlü performans, tedarik yöneticilerinin, özellikle metal parçaların aşındığı veya proses ortamıyla reaksiyona girdiği durumlarda bileşen arızalarını azaltmasını sağlar.
Ekibim, 316L çeliğin yerini alan kimyasal ekipmanlar için alüminyum borular ve burçlar tedarik ederek, 18 aydan uzun süre boyunca sıfır görünür bozulma ile kesintisiz hizmet sağladı; bu, metallerin ulaşamayacağı bir başarıdır. Ayrıntılı bağımsız testler, aşağıdakilerle vurgulanmıştır: Alüminyum oksit hakkında Vikipedi , olağanüstü olduğunu onaylayın kimyasal atalet ve uzun vadeli termal güvenilirlik. Bu benzersiz özellikler, akışkan işleme, elektronik üretimi ve laboratuvar cihazları gibi sektörlere uygundur.
Mülk | Alümina Seramik | Metal Alaşımı (316L SS) |
---|---|---|
Sertlik (Vickers, HV) | 1500–2000 | 180–250 |
Maksimum Sürekli Kullanım Sıcaklığı (°C) | 1600'e kadar | 600 |
Kimyasal Direnç | Mükemmel (asitler, alkaliler) | Orta ila İyi |
Aşınma Oranı (mg/1000 rev, ASTM G65) | 0,2–0,5 | 3–8 |
Alıcılar Yüksek Performanslı Seramiklerle Hangi Yaşam Döngüsü Kazanımlarını Elde Ediyor?
**Yüksek saflıkta alümina** bileşenleri kullanan alıcılar, belirgin şekilde daha uzun çalışma ömürlerine sahiptir. Gelişmiş seramikler, pompa contalarında, fırın borularında ve elektrik izolatörlerinde metallerden rutin olarak 5-10 kat daha uzun ömürlüdür, bu da plansız değişimleri en aza indirir ve ekipman çalışma süresini en üst düzeye çıkarır. Örneğin, Avrupa'daki bir sıvı işleme hattında alüminaya geçiş, değiştirme gerektirmeyen çalışma ömrünü 9 aydan 20 aya iki katına çıkarmıştır.
Bu dayanıklılık sayesinde, ileri teknoloji alıcıları üç doğrudan alanda tasarruf elde ediyor: azalan yedek parça stoğu, parça değişimlerinde harcanan daha az işçilik ve üretim programlarında daha az kesinti. AZoM'un seramik dayanıklılığına ilişkin incelemesi Ağır sanayide operasyonel güvenilirlik, TCO'nun temel etkenidir.
Ekipman Parçası | Metal Parça Ort. Ömrü (ay) | Alümina Parça Ort. Ömrü (ay) | Çalışma Süresi Kazancı (%) |
---|---|---|---|
Pompa Şaft Kovanı | 10 | 45 | +350% |
Fırın Borusu | 6 | 30 | +400% |
Elektrik İzolatörü | 30 | 120 | +300% |
Alüminaya Geçiş Bakım Maliyetlerini Azaltabilir mi?
Kesinlikle—alümina seramiklerin benimsenmesi, tedarik ve bakım ekiplerine ölçülebilir maliyet düşüşleri sağlar. Aşınmaya ve kimyasal saldırıya dayanıklı olan alümina parçalar, beklenmedik değişim veya plansız onarımlara nadiren ihtiyaç duyar. Yaygın bir bulgu: Metal burçlardan alüminaya geçiş, ortalama yıllık parça değişim döngüsünü altıdan bire düşürerek hem malzeme hem de işçilik maliyetlerinden tasarruf sağlar.
Endüstriyel alıcılarımız, standart 3 yıllık bir süre boyunca, yüksek hassasiyetli seramik çözümlerle bakım harcamalarının %40-70 oranında azaldığını doğruluyor. Bu sonuç, daha az hat kesintisi, daha az manuel müdahale ve daha düşük maliyetli arıza süresi riskini de hesaba katıyor; bu da ekipman filolarında **daha düşük TCO** için belirleyici bir kanıt.
Bakım Metriği | Geleneksel Metal | Alümina Seramik | Tipik 3 Yıllık Tasarruflar |
---|---|---|---|
Yıllık Değiştirme Etkinlikleri | 5–7 | 1–2 | %40–70 |
Çalışma Saati Harcaması (yılda) | 50–75 | 12–20 | %60'a kadar |
Yedek Envanter Talebi | Yüksek (4–8 set) | Düşük (1–2 set) | %60–80 |
Alümina Seramiklerin Yatırım Getirisini Kanıtlayan Vaka Çalışmaları Nelerdir?
Ekipman üreticilerinin gerçek dünya sonuçları, alüminyumun yüksek ön fiyatının, işletmedeki hızlı geri ödeme ile dengelendiğini kanıtlıyor. Örneğin, Mart 2024'te bir Alman hassas pompa OEM'i (Endress+Hauser, bkz. dava detayı ) paslanmaz çelik burçlardan CSCERAMIC'in %99,7 alüminyum oksit burçlarına yükseltildi. Sonuç: değiştirme aralığı 10 aydan 60 aya çıkarıldı, yıllık bakım maliyeti 9.500 € azaldı ve 20.000 saatlik deneme süresince beklenmedik proses arızaları ortadan kaldırıldı.
Başka bir örnek: ABD merkezli bir analitik cihaz şirketi (Thermo Fisher, 2024 1. çeyrek raporu), yüksek sıcaklık fırın tüpleri için yüksek saflıkta alüminaya geçti. Geçişten önce, tüp arıza oranı aylık değişimleri zorunlu kılıyordu; yükseltmeden sonra ise geçiş aralığı sıfır kusurla 18 aya uzadı ve üretim hattı başına yıllık 32.000 dolar tasarruf sağlandı.
Şirket | Başvuru | ROI Sürücüsü | Doğrulanmış Fayda |
---|---|---|---|
Endress+Hauser | Pompa burçları (kimyasal) | Uzun süreli çalışma, kısa bakım | 9.500 €/yıl, sıfır arıza (20.000 saat) |
Termo Fisher | Fırın boruları | Daha az hat durağı, uzun tüp ömrü | Yılda 32.000$/satır tasarruf edildi |
Alümina seramikler, alıcıların daha uzun ekipman ömrü ve ölçülebilir, uzun vadeli maliyet düşüşleri elde etmelerini sağlar. Küresel OEM filolarındaki kanıtlanmış başarı geçmişiyle, yatırım her kritik sektörde güvenilir yatırım getirisi sağlar.
Bize e-posta gönderin İletişim Sayfası